特集 物流現場改善のすすめ
(2018/5/9掲載) |
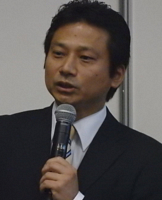
~執筆者紹介~
株式会社ロジスティクス・サポート&パートナーズ 常務取締役 石橋 岳人
神奈川大学経済学部経済学科卒。大学卒業後、株式会社船井総合研究所入社、流通業を中心としたコンサルティング活動・指導業務を経て、1998年、物流コンサルティング会社入社。同社取締役を経て、2005年1月、ロジスティクス・サポート&パートナーズ常務取締役に就任。
物流ABCを活用した利益の出せる得意先・作業管理の仕組みづくりや、物流企業の提案営業指導を得意としている。また、「見える化」手法を活用した“人時生産性”・“物流品質”・“モチベーション”に関する改善指導は好評を博している。
JILS 物流技術管理士資格認定講座 講師、大阪産業大学 非常勤講師
1.「良い」物流センターの運営とは何か?
例えば、下記のような物流センターAとBがあるとする。
どちらのセンターの方が良いセンターだと思うだろうか?
物流センターA 物流センターB
最高出荷生産性 170 130
平均出荷生産性 100 98
最低出荷生産性 60 85
この両センターについての評価は、センター運営能力としてはセンターBが高い、出荷能力&改善余力としてはセンターAが高いと評価する。
「良い」物流センターの運営を、より具体的に表現すれば、「ローコスト」で「高品質」な物流センターであると言い換えることができる。 そして、ローコストかつ高品質な運営環境をもたらす要素の一つが、「人時生産性の安定(平準)化」である。 人時生産性とは現場作業員1人の1時間当たりにおける作業能力を示す指標であり、「作業(活動)量÷延べ作業時間(作業人員×作業時間)」によって算出される。
人時生産性が安定(平準)化されているということは、毎日同じような作業スピードで業務を行うことができるため、ミスは発生しにくくなる。 また、作業日によって繁閑差がないということは、作業員間の不平不満をある程度抑えることができる。 しかしながら、人時生産性が安定(平準)化されている物流現場はそれほど多くないというのが現実である。
どちらのセンターの方が良いセンターだと思うだろうか?
物流センターA 物流センターB
最高出荷生産性 170 130
平均出荷生産性 100 98
最低出荷生産性 60 85
この両センターについての評価は、センター運営能力としてはセンターBが高い、出荷能力&改善余力としてはセンターAが高いと評価する。
「良い」物流センターの運営を、より具体的に表現すれば、「ローコスト」で「高品質」な物流センターであると言い換えることができる。 そして、ローコストかつ高品質な運営環境をもたらす要素の一つが、「人時生産性の安定(平準)化」である。 人時生産性とは現場作業員1人の1時間当たりにおける作業能力を示す指標であり、「作業(活動)量÷延べ作業時間(作業人員×作業時間)」によって算出される。
人時生産性が安定(平準)化されているということは、毎日同じような作業スピードで業務を行うことができるため、ミスは発生しにくくなる。 また、作業日によって繁閑差がないということは、作業員間の不平不満をある程度抑えることができる。 しかしながら、人時生産性が安定(平準)化されている物流現場はそれほど多くないというのが現実である。
2.改善のアプローチ:省時間と省工程
“現場改善”というと大半の人が『作業手順(工程)の見直し』をイメージするが、実はその前にすべき改善手法があることを忘れてはならない。『省時間』すなわち作業員コントロール(レイバーマネジメント)である。
作業生産性の向上は本来、『省時間』と『作業工程の見直し』の両面から捉えていくべきところ、多くの人が作業工程効率化(省工程)を想起し、“いかに作業手順を効率化するか?”のみに重点を置いて作業や現場環境を見直しているといえる。工程改善の手法としては物流ABCによって工程効率を可視化し、無駄を定量化することで改善につなげることができる。しかしながら工程改善には「システム改変」を伴うことが多いのも実際問題として挙げられる。
例えば、オーダーピッキングをトータルピッキング+仕分け方式に変更する場合には帳票出力などの変更が発生する。工程分析+改善手法の立案+システム改修となれば、作業改善の立案から実行までの時間が非常に長くかかることも推定される。 結果が出るのに半年~1年以上も要する取り組みでは、社内の改善プロジェクトチームは評価されにくくなってしまう。
そこで『省工程』よりも素早い改善が実現可能な『省時間』に取り組む必要が出てくる。(表1参照)
【表1】
作業生産性の向上は本来、『省時間』と『作業工程の見直し』の両面から捉えていくべきところ、多くの人が作業工程効率化(省工程)を想起し、“いかに作業手順を効率化するか?”のみに重点を置いて作業や現場環境を見直しているといえる。工程改善の手法としては物流ABCによって工程効率を可視化し、無駄を定量化することで改善につなげることができる。しかしながら工程改善には「システム改変」を伴うことが多いのも実際問題として挙げられる。
例えば、オーダーピッキングをトータルピッキング+仕分け方式に変更する場合には帳票出力などの変更が発生する。工程分析+改善手法の立案+システム改修となれば、作業改善の立案から実行までの時間が非常に長くかかることも推定される。 結果が出るのに半年~1年以上も要する取り組みでは、社内の改善プロジェクトチームは評価されにくくなってしまう。
そこで『省工程』よりも素早い改善が実現可能な『省時間』に取り組む必要が出てくる。(表1参照)
【表1】
3.省時間:作業員コントロール
『作業員コントロール』における改善の視点は、“現行の運営方法の中でいかに生産性を平準化するか”に重きを置き、工程間や日々の繁閑差の解消や人への気配りを行うことで、生産性の高位安定化を図る手法である。確かに物流現場では工程間や日々の繁閑差の解消を“経験則”的に実行してはいる。しかし、それはあくまでも属人的かつ職人技に頼った仕組みであり、定量的なアプローチができておらず、実態分析を行うとまだまだ改善の余地があるのが実情である。裏を返せば現行の作業工程(方法)を変更せずとも、運営をコントロールするだけで生産性の改善余地があることになる。故に工程改善よりも先に取り組むべきファクターと位置付けられる。
人時生産性が平準化していない主な理由としては、①経験則により想定物量に合わせた人員を予定しているが、実際の物量との乖離が発生した、②物量に合わせた作業パフォーマンス(忙しいときには頑張るが、暇なときには出荷可能時間までに終わればよいという動き方)、③多能工化により工程別作業時間の収集ができない――ことが挙げられる。
人時生産性を平準化するに当たっては、『ベンチマークすべき人時生産性の設定(目標生産性)』が運営力を左右する。日々の生産性を取得すると平均値、最高値、最低値が見えてくる。目標生産性に「最高値」や「平均値の20%向上」などといった設定を行う現場もあるが、「最高値」設定の場合には現場に対する負荷が高くなり過ぎてモチベーションの低下につながる危険性がある。また「平均値の20%向上」のような設定は作業的・視覚的にも分かりやすいが、一方で目標数値の根拠が薄くなるといったデメリットも持ち合わせている。こうした点を鑑み、『ハイアベレージ』(造語)という考え方を推奨している。
人時生産性が平準化していない主な理由としては、①経験則により想定物量に合わせた人員を予定しているが、実際の物量との乖離が発生した、②物量に合わせた作業パフォーマンス(忙しいときには頑張るが、暇なときには出荷可能時間までに終わればよいという動き方)、③多能工化により工程別作業時間の収集ができない――ことが挙げられる。
人時生産性を平準化するに当たっては、『ベンチマークすべき人時生産性の設定(目標生産性)』が運営力を左右する。日々の生産性を取得すると平均値、最高値、最低値が見えてくる。目標生産性に「最高値」や「平均値の20%向上」などといった設定を行う現場もあるが、「最高値」設定の場合には現場に対する負荷が高くなり過ぎてモチベーションの低下につながる危険性がある。また「平均値の20%向上」のような設定は作業的・視覚的にも分かりやすいが、一方で目標数値の根拠が薄くなるといったデメリットも持ち合わせている。こうした点を鑑み、『ハイアベレージ』(造語)という考え方を推奨している。
4.KPI:「ハイアベレージ」による合理的な目標値設定
『ハイアベレージ』とは、日々の生産性数値に対して平均値を超えるデータ(作業日)を対象に再度平均化した数値のことである。本来、同じ業務を日々行う物流現場において人時生産性は平準化されるべきであるが、作業物量の変動や運営状況などにより変化する。人時生産性を落としているのは平均以下の作業日における人員配置であり、作業量に応じた人員配置ができれば自ずと平均値は上がることになる。
つまり現場への改善モチベーションとして「いつでも最高値(繁忙日)」を目指すのではなく、平均以下を除いた「平均超の作業日における平均値」を目標とした場合には、無理をさせ過ぎずに日々の業務に向かうことができると考える。 『改善余地』とは目標値(ハイアベレージ)と平均以下の生産性における差であり、人時生産性の波動(最高値と最低値の差)が大きければ大きいほど改善余地は大きくなる。人時生産性の波動があまり大きくない現場については、既に『省時間』の改善ステップは完了しているということになり、次の『省工程』に進むことで更なる作業改善を実現することになる。
人時生産性の平準化によって、作業現場における人員のモチベーションを向上させることもできるだろう。実際の現場では作業日(例えば曜日別や旬別・月別)によって人時生産性の傾向は出ており、例えば特定曜日しか出勤しないパートタイマー社員が “自分は忙しい曜日に出ているのに、あの人は暇な日しか来ていない。それなのに同じ時給なのは納得が行かない”ということが発生している。こうした不公平感も人時生産性が平準化されることで改善・解消される。
冒頭に示した2つのセンターにおいては、物流センターAは、最高出荷生産性と最低出荷生産性の差が大きいことから、現場の負荷は高いと言わざるを得ない。しかし、最高出荷生産性は、物流センターBよりも高いことから、現行の作業方法でのポテンシャルは高いということになる。 このため、物流センターAでは、まずは作業員コントロールのみで作業効率を上げ、その上で工程改善を行い更に効率向上を図る。物流センターBについては、最高と最低の出荷生産性に差が小さいことから、現行の作業方法での限界が近づいており、工程改善のアプローチが必要となる。ただし、現場運営は、物流センターBの方が良い雰囲気で運営できていることは容易に想像ができる。
物流現場での人材確保が困難になってきている現在、人時生産性の安定化による職場モチベーションの維持向上は、必須の要件となっている。
つまり現場への改善モチベーションとして「いつでも最高値(繁忙日)」を目指すのではなく、平均以下を除いた「平均超の作業日における平均値」を目標とした場合には、無理をさせ過ぎずに日々の業務に向かうことができると考える。 『改善余地』とは目標値(ハイアベレージ)と平均以下の生産性における差であり、人時生産性の波動(最高値と最低値の差)が大きければ大きいほど改善余地は大きくなる。人時生産性の波動があまり大きくない現場については、既に『省時間』の改善ステップは完了しているということになり、次の『省工程』に進むことで更なる作業改善を実現することになる。
人時生産性の平準化によって、作業現場における人員のモチベーションを向上させることもできるだろう。実際の現場では作業日(例えば曜日別や旬別・月別)によって人時生産性の傾向は出ており、例えば特定曜日しか出勤しないパートタイマー社員が “自分は忙しい曜日に出ているのに、あの人は暇な日しか来ていない。それなのに同じ時給なのは納得が行かない”ということが発生している。こうした不公平感も人時生産性が平準化されることで改善・解消される。
冒頭に示した2つのセンターにおいては、物流センターAは、最高出荷生産性と最低出荷生産性の差が大きいことから、現場の負荷は高いと言わざるを得ない。しかし、最高出荷生産性は、物流センターBよりも高いことから、現行の作業方法でのポテンシャルは高いということになる。 このため、物流センターAでは、まずは作業員コントロールのみで作業効率を上げ、その上で工程改善を行い更に効率向上を図る。物流センターBについては、最高と最低の出荷生産性に差が小さいことから、現行の作業方法での限界が近づいており、工程改善のアプローチが必要となる。ただし、現場運営は、物流センターBの方が良い雰囲気で運営できていることは容易に想像ができる。
物流現場での人材確保が困難になってきている現在、人時生産性の安定化による職場モチベーションの維持向上は、必須の要件となっている。